
|
Select milling machine (postprocessor), set postprocessor options, enter axis boundary, enter values for calculating milling times.
Click here to create a new machine.
|
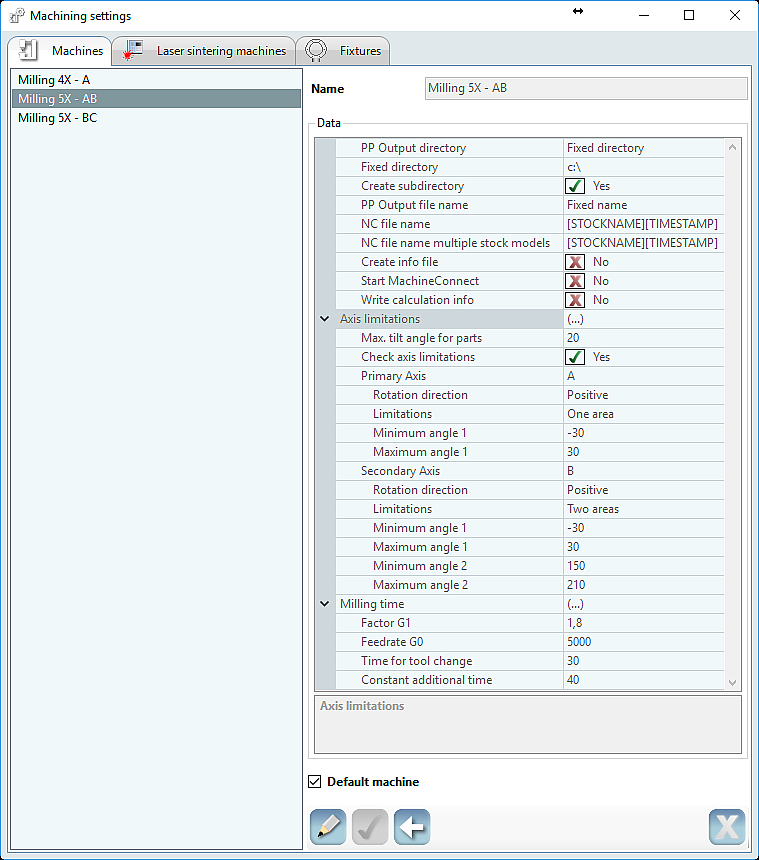
|
The selection window shows the [Machines] tab, which provides a list of machines, corresponding settings, and machining options: edit, apply, exit.
|
|
Machines
|
List of available machines
DIN ISO = standard machine.
|
|
Name
|
Name of the machining device.
|
Postprocessing
|
Defaults for NC programs.
|
|
|
Global
|
Same for all machines, according to the general settings.
|
|
Individual
|
Separate for each machine, with the following machine-specific settings.
|
|
Postprocessing strategy
|
Standard
|
|
|
Postprocessor type:
Standard or user-specific (option).
|
|
Postprocessing mode
|
Settings for calling up the postprocessor:
Start hyperVIEW.
Start hyperVIEW and proceed after the prompt.
Immediate postprocessing (run process in the background).
|
|
Tool-specific output
|
No
|
|
No
|
Output for all tools.
|
|
Yes
|
Tool-specific output.
|
|
PP output directory
|
Settings for the directory containing the NC file.
|
|
hyperDENT work directory
|
Same directory as for the hyperDENT calculations.
|
|
hyperVIEW configuration
|
Directory according to the hyperVIEW configuration.
|
|
Fixed directory
|
Specify a path name for the NC file.
|
|
Fixed directory
|
Path name: Drive and directory for the NC file.
|
|
Create subdirectory
|
Create subdirectory for the NC file in the output directory.
|
|
PP output file name
|
Settings for the name of the NC file:
|
|
hyperVIEW configuration
|
Name according to the hyperVIEW configuration.
|
|
Fixed name
|
Specify name of the NC file.
|
|
NC file name
|
|
|
Parameter for generating the name of the NC file:
|
[STOCKNAME] (name of blank)
[MODELNAME] (name of part)
[TIMESTAMP] (date, time)
[FIXTURENAME] (name of the fixture)
[MACHINENAME] (name of the machine)
[MATERIALNAME] (name of the material)
[BLANKTYPENAME] (name of the type of blank)
[BLANKEXTERNALID] (external blank ID)
[BLANKCHARGE] (batch of the blank)
[DATE] (date)
[TIME] (time)
[YYYY] (year, 4 digits)
[YY] (year, 2 digits)
[MM] (month of the year)
[DD] (day of the month)
[hh] (hour of the day)
[mm] (minute of the hour)
[ss] (second of the minute)
|
|
Create info file
|
Create file with program information.
If the project file has already been saved, a reference to the project file is provided in the NC info file.
|
Axis limitations
When using hyperDENT, you can configure machines in --> “Settings” > “Machining” > “Configure machine” such that axis limitations are already checked by hyperDENT during the calculation.
To do so, specify the rotation axis and rotational direction according to the machine to be used.
|
|
|
|
|
Max. tilt angle for parts
|
This value corresponds at most to the angle of the axis with the lowest possible deflection. The system attempts to tilt the part so that the required height is attained. The part height and the part-specific insertion directions are taken into account. When performing 5X simultaneous machining, make sure that there is still enough space for movement of the axes during machining. For example, the lowest axis can be 20 degrees and the maximum angle of inclination for parts can be 15 degrees when working with a 5-degree axis deflection during 5X machining.
|
|
Check axis limitations
|
|
|
Yes
|
Check the axes during calculation to see if axis limitations are exceeded.
|
|
No
|
No checks during calculation.
|
|
Primary Axis
|
|
|
None
|
There is no rotation axis.
|
|
A
|
Machine has an A-axis, i.e., rotation around X.
|
|
B
|
Machine has a B-axis, i.e., rotation around Y.
|
|
Rotation direction
|
|
|
Positive/Negative
|
Rotation direction of the axis.
|
|
Limitations
|
Scope of the limitation:
|
|
Unlimited
|
The axis has no angle limitation.
|
|
One area
|
The axis has an area to which it is limited.
|
|
Two areas
|
The axis has two areas to which it is limited.
|
|
Minimum angle 1
|
Smallest angle in area 1.
|
|
Maximum angle 1
|
Largest angle in area 1.
|
|
Minimum angle 2
|
Smallest angle in area 2.
|
|
Maximum angle 2
|
Largest angle in area 2.
|
|
Secondary axis
|
Additional 2nd rotation axis:
|
|
None
|
No secondary rotation axis.
|
|
A
|
The machine also has an A-axis, i.e., rotation around X.
|
|
B
|
The machine also has a B-axis, i.e., rotation around Y.
|
|
C
|
The machine also has a C-axis, i.e., rotation around Z.
|
|
Rotation direction
|
|
|
Positive/Negative
|
Rotation direction of the axis.
|
|
Limitations
|
Scope of the limitation:
|
|
Unlimited
|
The axis has no angle limitation.
|
|
One area
|
The axis has an area to which it is limited.
|
|
Two areas
|
The axis has two areas to which it is limited.
|
|
Minimum angle 1
|
Smallest angle in area 1.
|
|
Maximum angle 1
|
Largest angle in area 1.
|
|
Minimum angle 2
|
Smallest angle in area 2.
|
|
Maximum angle 2
|
Largest angle in area 2.
|
Milling time
Details for calculating the machining time.
|
|
Factor G1
|
1 ... 2
Time factor for the milling time with feedrate.
|
|
1
|
Milling time for G1 calculated according to defined feedrate.
|
|
>1 ... 2
|
Since the actual feedrate also depends on the machine dynamics and number of axes moved, it may be smaller, resulting in longer machining times.
Use the factor (based on experience) to take into account the deviation when calculating the machining time.
|
|
Feedrate G0
|
mm/min
Rapid traverse rate for calculating the time.
|
|
Time for tool change
|
s
Time for the tool change.
|
|
Constant additional time
|
s
Time offset that is added to the calculated machining time, e.g., for tool changes.
|
|
Default machine
|
Use selected machine as default.
|
|